<2024 New Edition> Semi-Solid Battery Technology: Development and Future Prospects
Major battery manufacturers and automotive OEMs are planning to mass-produce all-solid-state batteries. However, large-scale production of these batteries is expected to take 5-10 years. In the meantime, there's increasing interest in semi-solid-state batteries due to their potential safety, longevity, and cost advantages over conventional lithium-ion batteries (LiBs). This anticipation is driving many companies, especially in China, to announce mass production plans for semi-solid-state batteries.
Semi-solid-state batteries serve as a transitional product between liquid-state and solid-state batteries. They incorporate a portion of electrolyte within the battery to enhance the interface. Compared to liquid-state batteries, semi-solid-state batteries necessitate minimal alterations to the material system, utilize separators and liquid electrolytes, and can decrease the volume of liquid electrolyte present. This reduction can enhance battery energy density and safety. Moreover, the manufacturing processes for semi-solid-state batteries closely align with traditional lithium-ion battery techniques and equipment.
In semi-solid-state batteries, the addition of a liquid can enhance ion transport through the composite material without compromising electron transport, leading to improved electrochemical performance of the electrodes. This requires a low-resistance ion transport through the solid/liquid interface. Recent in-situ polymerization techniques have been employed to reduce the liquid content by solidifying the original liquid components of the semi-solid-state battery.
Organic-inorganic composite solid electrolytes, one of the most prevalent forms in semi-solid-state batteries, combine the advantages of both organic and inorganic solid electrolytes. These composite materials, typically consisting of oxide solid electrolytes and polymer electrolytes, exhibit exceptional tensile strength and mechanical properties, excellent processability, and adequate ion conductivity, making them suitable for large-scale production.
The development of semi-solid-state batteries is primarily being driven by Chinese companies, including CATL, WeLion, Qingtao Energy, Ganfeng Lithium, Guoxuan, Farasis, and Tailan. Additionally, LGES, Factorial Energy, SES, and ProLogium are also independently or collaboratively developing this technology with automotive OEMs.
At the 2023 Shanghai Auto Show, CATL unveiled its highly anticipated Condensed Battery, grabbing industry attention. This groundbreaking technology utilizes a high-power bionic condensed electrolyte and features an adaptive micro-level network structure. These innovations enhance dynamic performance and lithium ion transport efficiency, resulting in an impressive cell energy density of 500 Wh/kg, surpassing conventional lithium-ion batteries. Moreover, CATL's innovation extends to stability and production capabilities, promising a reliable and scalable solution for electric vehicles in the future.
The application of solid-state batteries has already begun, and the NIO ET7 equipped with WeLion's 360Wh/kg semi-solid-state battery, boasting 150kWh, achieved a range of 1145km, surpassing conventional batteries. It's reported that mass production started in April 2024.
According to SNE Research, global solid-state battery production capacity is expected to reach approximately 168GWh by 2030 and 300GWh by 2035. In terms of overall battery market share, it is projected to peak at around 6.55% in 2033 from approximately 5.7% in 2030, before declining to 5.7% again by 2035 as solid-state batteries are widely adopted.
The strong points of this report are as follows.
① Detailed coverage of recent trends surrounding semi-solid-state batteries
② Detailed coverage of major battery manufacturers and automotive OEMs
③ Navigating the Competitive Landscape: Semi-Solid-State Batteries vs. Solid-State Batteries
④ The development history and current status of semi-solid-state batteries
⑤ Analysis of key patents related to semi-solid-state batteries
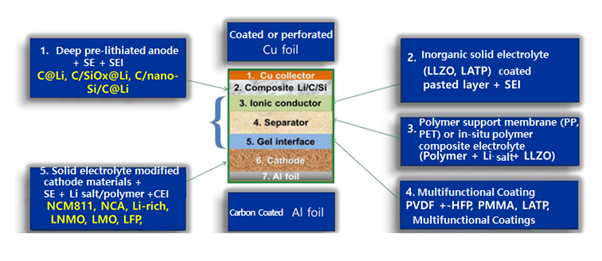
(WeLion New Energy's in-situ solidification-based semi-solid-state battery system)
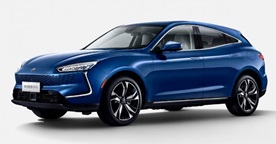
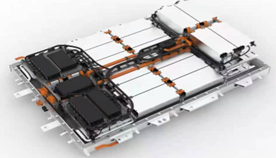
(Dongfeng Motor's Seres 5 SUV and the 80~90kWh semi-solid-state battery pack provided by Ganfeng Lithium)
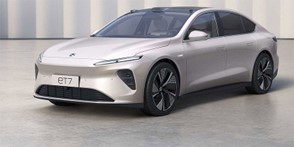
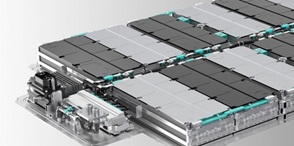
(The Nio ET7 150kWh EV car equipped with semi-solid-state batteries) (Nio ET7 150 kWh semi-solid-state battery pack, 1,000 km range)
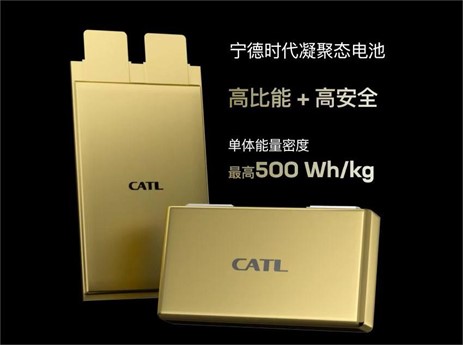
(CATL’s condensed battery)
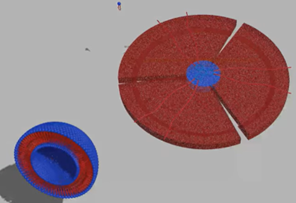
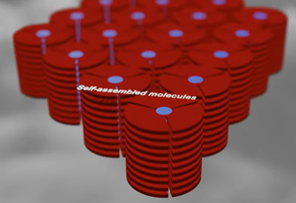
(The polymer speculated to be used in CATL's condensed battery, based on patents filed by CATL, and the self-assembled molecule structure constructed from it. It is anticipated to enhance Li+ mobility.)
Table of Contents
1. Semi-Solid-State Battery Development Trends 11
1.1. Commercialization Challenges for All-Solid-State Batteries 16
1.1.1. . Immaturity of All-Solid-State Battery Manufacturing 17
1.2. Semi-Solid-State Batteries: Impact on the Industrial Chain 17
1.2.1. Modifications to the Packaging Process: Intermediate and Rear Stages 17
1.2.2. Solid Electrolyte Film Formation Process 18
1.2.3. Innovation in Core Material Systems 19
1.2.3.1. Polymer Systems 19
1.2.3.2. Oxide Systems 21
1.2.3.3. Sulfide Systems 25
1.2.3.4. Costs 27
1.2.3.5. Electrolyte 27
1.2.3.6. Anode Material 29
1.2.3.7. Binders 29
1.2.3.8. Pre-lithiation 30
1.2.3.9. Separators 31
1.2.3.10. Dry Electrode Process (DBE) 32
1.2.3.11. Industrialization Status of Semi-Solid Batteries 33
1.2.3.12. Gel-Type Solid Electrolyte 34
1.3. Reducing the Cost of Semi-Solid-State Batteries 35
1.3.1. Using Lithium Metal Anodes 36
1.3.2. Need for Economies of Scale 37
1.4. Semi-Solid State Batteries: Key Advantages 37
2. Classification of Solid-State, Semi-Solid-State, and Hybrid Batteries 39
2.1. Types of Solid Electrolytes 39
2.2. Classification of Electrolyte Systems 42
2.3. Classification of Solid Electrolytes and Their Pros and Cons 43
2.4. Types of Hybrid Electrolyte 43
2.5~7. Properties of Hybrid Electrolyte 44
2.8. Hybrid Inorganic Polymer Composite Electrolyte (IPC) 45
2.9~10. Organic-Inorganic Hybrid Solid-State Electrolyte 46
3. Polymer/Inorganic Composite Electrolytes for Semi-Solid-State Batteries 48
3.1. Overview 48
3.2. Introduction 49
3.2.1. Lithium Ion Conductivity 52
3.2.2. Electrochemical Stability 53
3.2.3. Dendrite Suppression 54
3.2.4. Contact Stability 55
3.3. Polymer/Inorganic Composite Electrolyte Fillers 56
3.3.1. Components of Polymer/Inorganic Composite Electrolytes 56
3.3.2. Inert Fillers 57
3.3.2.1. Oxide Fillers 59
3.3.2.2. Ferroelectric Fillers 59
3.3.2.3. Porous fillers 60
3.3.2.4. Other Inert Fillers 61
3.3.3. Active Fillers 62
3.3.3.1. Garnet-Type Solid Electrolytes 62
3.3.3.2 NASICON-Type Solid Electrolytes 65
3.3.3.3. Perovskite-Type Solid Electrolytes 68
3.3.3.4. Sulfide-Type Solid Electrolyte 69
3.3.4. Synthesis of Polymeric/Inorganic Complex Electrolytes 71
3.4. Conclusion and Summary 72
4. In-Depth Analysis of All/Semi-Solid-State Batteries 73
4.1. All/Semi-Solid-State Battery Advantage (Energy Density) 74
4.2. All/Semi-Solid-State Battery Advantage (Safety) 75
4.3. Semi-Solid-State Batteries Disadvantage 76
4.4. Semi-Solid-State Battery Costs and Future Outlook 77
4.5. All/Semi-Solid-State Battery Policies by Country 78
4.6. All/Semi-Solid-State Battery Application Market 79
4.7. Semi-Solid-State Battery Application Trends 80
4.8. Oxide Solid Electrolyte Production Capacity by Company 81
5. Semi-Solid-State Batteries: The Optimal Solution for EVs? 83
5.1. Semi-Solid-State Batteries vs. Other Batteries 83
5.2. Semi-Solid-State Battery Industry Chains 83
5.2.1. Cathode/Anode Materials 84
5.2.2. Solid Electrolytes 84
5.2.3. EV Market 85
5.2.4. Market Analysis (Chinese Market) 85
6. Quasi-Solid Lithium Battery Development: Interlayer Application 87
6.1. Research Overview 87
6.2. The Role of the Interplayer 88
6.3. Integrating Ag-C Composites into LLZTO 92
6.3.1. Introducing Additional Layers 93
6.3.2. Enhancement of Ag Adhesion 93
6.4. Analysis of Lithium Metal Cell Characteristics 94
6.4.1. Electrochemical Cell 94
6.4.2. .Electrochemical Performance of LLZTO 96
6.4.3. Li|Ag-C/Ag/LLZTO/IL|LCO Cell 99
6.5. Conclusion and Discussion 101
7. Solid-State Battery Hybrid Interface (SLEI) 102
7.1. Definition of SLEI(Solid-Liquid Electrolyte Interphase) 102
7.2. Difference between LIBs and All-Solid-State Batteries 102
7.3. Hybrid Solid Electrolyte/Liquid Electrolyte(SE/LE) Systems 104
7.4. Similarities and differences between SLEI and SEI 105
7.5. Oxide-Based Hybrid System 106
7.6. Sulfide-Based Hybrid System 108
7.6.1. Research on Pristine Solvents 109
7.6.2. Electrochemical Performance for Liquid Electrolytes 110
8. High-Efficiency Li Metal Batteries with Quasi-Solid Electrolytes (Introduction of MOFs) 113
8.1. Research Overview 113
8.2. Fabrication of Quasi-Solid Electrolytes 116
8.2.1. CuBTC MOF as a Host Material 116
8.2.2. Physicochemical Properties of Quasi-Solid Electrolytes 118
8.2.3. Compatibility of Quasi-Solid Electrolytes with Electrodes 120
8.2.4. Electrochemical Performance of NCM-811//Li Pouch Cells 125
8.3. Conclusion 127
9. Li-S Batteries with Quasi-Solid Electrolytes 128
9.1. Li-S Battery Overveiw 128
9.2. Solid-State Li-S Batteries 129
9.2.1. Operating Principle 129
9.2.2. . Charge/Discharge Profile 130
9.2.3. Ion Conduction Mechanisms 130
9.2.4. Technical Issues 131
9.3. Electrolyte Material Design Strategies 131
9.4. Polymer Electrolyte Applications 132
9.4.1. Gel/Quasi-Solid Polymer Electrolyte 132
9.4.2. Solid-Polymer Electrolyte 134
9.5. Inorganic Solid Electrolyte 136
9.5.1. Sulfide Solid Electrolyte 137
9.5.2. Oxide Solid Electrolyte 138
9.6. Hybrid Electrolyte 139
9.6.1. Inorganic-Organic Composite Electrolyte 139
9.6.2. Inorganic Solid-Liquid Electrolyte 139
9.7. Conclusion and Outlook 140
10. Semi-Solid-State Battery Industry Trends 143
10.1. The State of Semi-Solid-State Batteries in China 143
10.2. .All-Solid-State Battery R&D in China 144
10.3. Each Company's Investment Status 145
10.4. Outlook on All(Semi)-Solid-State Batteries in China 146
10.5. Commercialization of Next-Generation Batteries 147
10.5.1. Limitations in Improving Current LiBs 148
10.5.2. Continued Development of Semi-Solid-State Batteries 149
10.5.3. Growing Recognition of Semi-Solid-State Batteries 151
10.5.4. Solid-State Battery Production from 2026 152
10.5.5. Japanese Companies Lagging Behind by 3-7 Years 153
10.5.6. Global Trends in Semi-Solid-State-Batteries 153
10.5.7. Trends in Cathode/Anode Material Development 156
10.5.8. Demodularization of the Battery Structure 157
10.5.9. Mass Production of Semi-Solid-State Batteries Initiated 160
11. Semi-Solid-State Battery Manufacturers and Operations 162
11.1. LGES 162
11.2. SK On 163
11.3. WeLion 163
11.4. BAK 165
11.5. CATL 166
11.6. NIO 168
11.7. KAERI(Korea) 174
11.8. ProLogium 175
11.9. SES 178
11.10. Factorial Energy 179
11.11. KIERKorea) 181
11.12. imec 182
11.13. Qingtao Energy 183
11.14. Ganfeng Lithium 185
11.15. Yiwei Lithium Energy (EVE) 186
11.16. Guoxuan Hi-Tech 187
11.17. Farasis Energy 188
11.18. SVOLT 189
11.19. SEMCORP 190
11.20. NGK 191
11.21. Kyocera 195
11.22. Talent New Energy 199
12. Semi-Solid State Battery Market Outlook 200
12.1. Current Status of Semi-Solid-State Battery Industry in China 200
12.2. History of Semi-Solid-State Battery Industry 200
12.3. Policies for China's Semi-Solid-State Battery 201
12.4. China's Semi-Solid-State Battery Demand Outlook for EVs 201
12.5. Market Penetration Rate of Semi-Solid-State Batteries in China 202
12.6. Global Semi-Solid-State Battery Market Outlook 202
13. Patent Analysis of Semi-Solid-State Batteries 205
13.1. Korea Institute of Energy Technology 205
13.2. Qingtao New Energy 210
13.3. LGES 212
13.4. Arkema 214
13.5. Global Graphene Group Inc. 216
13.6. WeLion New Energy 217
13.7. Ganfeng Lithium 219
13.8. Sion Power 221
13.9. Factorial Energy 223
13.10. StoreDot 226
13.11. SVOLT 229
References 232