Lithium-ion batteries (LIBs) are one of the
most promising energy storage devices to address the growing demand for energy
storage in electric vehicles and hybrid devices due to their high energy and
power density, and their use is increasing rapidly with the growing interest in
utilizing green energy for carbon reduction.
According to SNE Research, after the rapid
development of new energy storage devices and electric vehicles, the demand for
LIBs has been steadily increasing, and the electric vehicle battery market size
is expected to grow from $196B in '25 to $401B in '30, with a CAGR of 21%.
The characteristics of LIBs are highly
dependent on the electrodes, and optimizing the electrode structure is a top
priority to achieve superior battery performance. While the active materials of
the anode and cathode are currently being studied and examined with great
interest in commercialized LIBs as well as in research, the inactive binder,
which maintains the integrity of the electrode and supports the electrochemical
process at a low weight fraction (≤5wt%), occupies a critical position in the
performance of the electrode along with the active materials and conductors,
but has received less attention compared to its importance.
Although binders are a very small part of
the electrode, they play a critical role in determining the overall performance
of the electrode. The binder is responsible for the adhesion of the anode and
cathode active materials to the respective pole plates of the collector and for
their durability. The binder must be (1) electrochemically stable in the
electrolyte, (2) flexible and insoluble, and (3) resistant to corrosion by
oxidation, especially for cathode binders.
Therefore, a functional binder with high
bond strength and elasticity is required to effectively connect the active
material and the conductor to the collector and accommodate volume expansion to
ensure good electrode structure during charge and discharge. Recently, with
more insights into binder screening and design, the focus of research is
shifting from a mechanical stabilization perspective to multifunctionality that
provides electrochemical benefits as well as structural support.
Recently, with the increasing adoption of
silicon cathode materials, a new generation of research is underway, as studies
have shown that binders have a significant impact on the lithiation reaction,
helping to improve electrode capacity and cycleability. Conventional binders
mainly use PVDF (PolyVinyliDeneFluoride), a fluoroplastic, for the cathode and
SBR (Styrene-Butadiene-Rubber) and CMC (Carboxyl Methyl Cellulose) binders, a
synthetic rubber, for the anode, but they are not suitable for use in silicon anodes
due to large volume changes.
PTFE (PolyTetraFluoroEthylene) binders have
been used for cathode materials, and water-based binders such as PAA
(PolyAcrylicAcid) and PI (PolyImide) have been attracting attention for anode
materials.
Binders such as PAA and PI are water-based
binders, which are used in silicon anode materials that use water-based
solvents as electrolytes. Compared to conventional binders, these binders have
high tensile strength, high adhesion, and are resistant to volume expansion of
silicon anode materials and form a stable SEI (Solid Electrolyte Interphase)
layer by wrapping the active material.
PTFE, a next-generation binder for cathode
materials, is a hydrophobic material with excellent chemical and heat
resistance and is expected to gain attention in dry electrode processes and
all-solid-state batteries.
PVDF binders are produced by Kureha in
Japan, Solvay in Belgium, and Arkema in France, and SBR binders are produced by
Zeon in Japan, all of which are expensive items with a high proportion of
foreign production.
The cathode binder is produced by Korea's
Chemtros, and for the anode binder, Korea's Hansol Chemical has successfully
localized it and is supplying it to Samsung SDI and SK On, while LG Chem. and
Kumho Petrochemical are also supplying cathode binders.
Meanwhile, SNE Research's global demand
forecast for binders for lithium-ion batteries is expected to increase from
89,000 tons in 2025 to 232,000 tons in 2030, with a value of about KRW 4.4
trillion in 2030.
High-energy-density batteries are expected
to place higher requirements on high-performance binders, and from this
perspective, binder design should consider the following.
(1) The binder
content should be less than or equal to 3 wt% of the total electrode mass
without losing mechanical strength and adhesion.
(2)
Simplification of synthesis using water-based and dry-based polymers from the
perspective of low cost and sustainability.
(3)
Multifunctional polymer binders that can integrate all necessary functions into
one polymer.
(4) Deep insights
into polymer dispersion and degradation mechanisms, and more.
In this report, SNE has summarized in
detail the information available in the literature on the design, synthesis,
and application of binders for lithium-ion battery electrodes and forecasted
the demand and market for binders based on our forecasts for lithium-ion
batteries, and quoted market size and forecasts from external research
organizations in the appendix to help readers understand the overall scale.
Finally, by summarizing the status of
binder manufacturers and their main products, we hope to provide a holistic
insight for researchers and interested parties in this field, which will help
to improve the performance of batteries, including their energy density, fast
charging capability, and long-term life characteristics.
Strong points
of this report
① Provides a
general overview of the binder and contains rich technical content
② Includes key
points to consider in design and synthesis through examples of binder
development.
③ Summarizes the
development status and case analysis of binders not only for LIBs but also for
next-generation batteries such as Li-S and all-solid-state batteries.
④ Provides
objective figures on the binder market through objective binder market
forecasts based on SNE Research's battery forecasts.
⑤ Detailed
information on the development status and product status of major binder
companies.
[Shipments and M/S of PVDF binder manufacturers]
[Shipments and M/S of SBR binder
manufacturers].
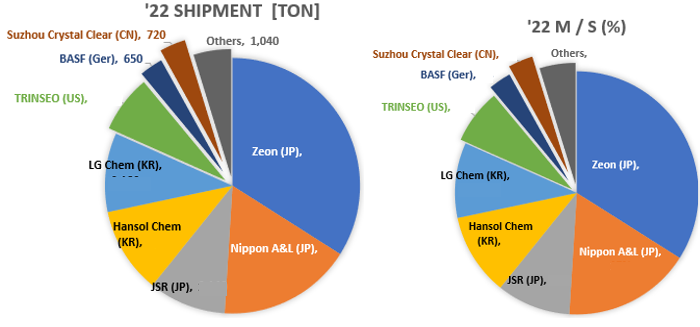
[Binder cost analysis for 4680 cells for Tesla].
• Cathode: NCM811, Anode: Si series
• PVDF cathode binder consumption and
cost for a 1 GWh cell: Approx. 38 tons, KRW 1.546 billion
• PAA anode binder consumption and cost
for a 1 GWh cell: Approx. 24 tons, KRW 0.823 billion
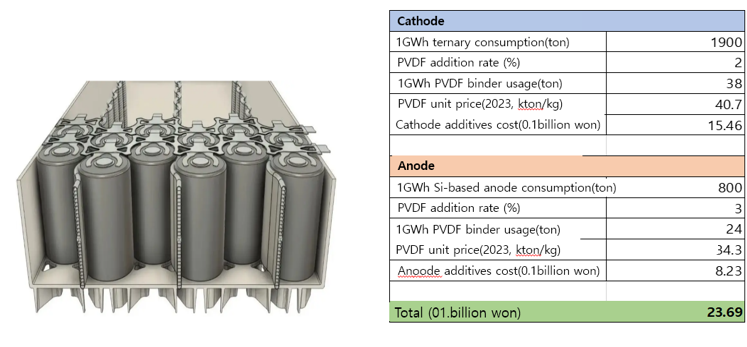
[A schematic of the dry and wet processes for electrode
fabrication].
1.1. Introduction
1.2. Definition,
Role, and Requirements
1.2.1.
Role and Features
1.2.2.
Requirements
1.3. Categories
and Types
1.3.1.
Types
1.4. Operation
Mechanism
2. Types of binders and
R&D practices
2.1. Binders for Cathodes
2.1.1. Non-Aqueous Binders
2.1.2.
Industry Status of PVDF Cathode Binders
2.1.3. (CMC+SBR)
Industry Status of Anode Binders
2.1.4. Water-based
Binders
2.1.5. Other binders
2.2. Binders for Anodes
2.2.1. Insertable Anode Binder
2.2.1.1. Binders for Graphite Electrodes
2.2.1.2. Anode Binder for LTO
2.2.2. Alloy Anode Binders
2.2.2.1. Linear Polymer Binders
2.2.2.2. Crosslinked Polymer Binders
2.2.2.3. Branched and Extra-Large Polymer Binders
2.2.2.4. Conductive Polymer Binders
2.3. Binder for Next-Generation Batteries (1)
2.3.1. Binders for Lithium-Sulfur (Li-S) Batteries
2.3.2. Binders for Dry Process
2.4. Binder for Next-Generation Batteries (2)
2.4.1. Binders for Solid Electrolytes
2.4.1.1. Overview of All-Solid-State
Batteries
2.4.1.2. Sulfide-based All-Solid-State Battery
Technology
2.4.1.3. Manufacturing of All-Solid-State Cells and
the Purpose of Binders
2.4.1.4. Binder Technology for Cathodes
2.4.1.4.1. Binder Technology for Wet Processes
2.4.1.4.2. Binder Technology for Dry Processes
2.4.1.5. Binder Technology for Electrolyte Layers
2.4.1.6. Binder Technology for Anodes
2.4.1.6.1. Binder Technology for Graphite-Based Anodes
2.4.1.6.2. Next Generation Binder Technology for
Anodes
3. Binder Market
3.1. Overall Outlook for the Binders Market
3.2. PVDF Market Outlook for Global LIBs
3.2.1. Global Battery Market Demand
3.2.2. Global LIB Battery Binder Demand Outlook
3.2.3. LIB Battery Binder Price Outlook
3.2.4. LIB Battery Binder Market Size Outlook
3.2.5. Global LFP Battery Demand and Cathode Material
Demand Outlook
3.2.6. PTFE for LFP Batteries Price and Market Outlook
3.2.7. PTFE Binder Usage for LFP Batteries
3.2.8. Market Outlook for Binders for Silicon-based
Cathodes
3.2.9. Silicon-based Anode Material Market Outlook
3.2.10. PAA Binders for Silicon Anode Market Outlook
3.2.11. Binder cost analysis for 4680 batteries for
Tesla
3.2.12. Shipments and M/S of PVDF Binder Manufacturers
3.2.13. Shipments and M/S of SBR Binder Manufacturers
3.2.14. Shipments and M/S of CMC Binder Manufacturers
4. Binder Manufacturer Status
[1] Arkema
[2] BASF SE
[3] Solvay
[4] Kureha
[5] ZEON
[6] JSR
[7] Fujian Blue Ocean Black Stone
[8] Dupont
[9] Ashland Inc
[10] MTI Corp.
[11] TRINSEO
[12] Xinxiang Jinbang Power Technology
[13] Lihong Fine Chemical
[14] Chemtros
[15] Hansol Chemical
[16] Kumho Petrochemical
[17] Daikin Industry
[18] Nanografi Nano Technology
[19] Nippon
Paper Group
[20] APV Engineered Coatings LLC
[21] Sichuan Indigo Materials Science & Technology
[22] Guangzhou
Songbai Chemical Co
[23] Nippon A&L Inc
[24] Daicel Miraizu Ltd
[25] Sinochem Group Co
[26] Ube Corp.
[27] AOT Battery Equipment Technology
[28] Shanghai 3F New Materials
[29] GL Chem
5. Appendix [For reference]
6. References